QUALITY
Quality Department
Department's Key Roles
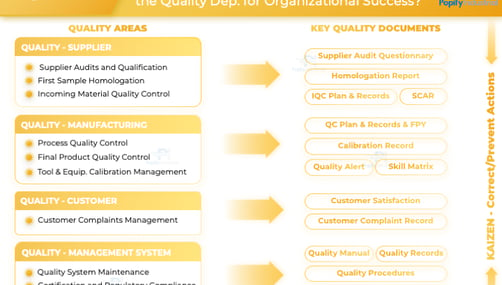
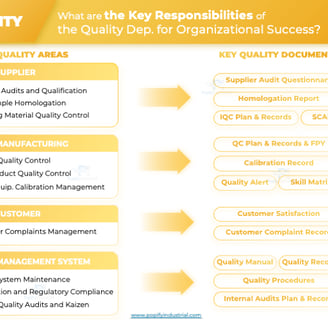
QUALITY | DEPARTMENT'S KEY ROLES
Essential Responsibilities of the Quality Department in Pursuing Organizational Success
Introduction
Quality is not just a benchmark; it is a fundamental commitment to excellence that ensures customer satisfaction and long-term business success. The Quality Dept. serves as the guardian of this commitment, implementing systems and processes that guarantee every product meets expectations.
1Supplier Quality: The First Line of Defense.
The quality of a final product begins long before manufacturing—it starts...
Please download the attached PDF or PPT to access the complete content.
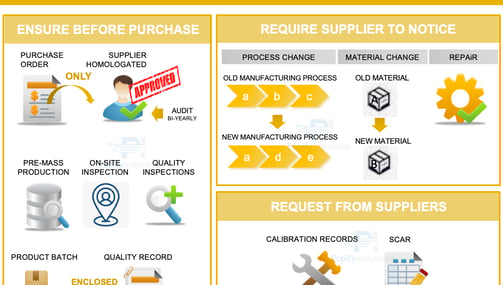
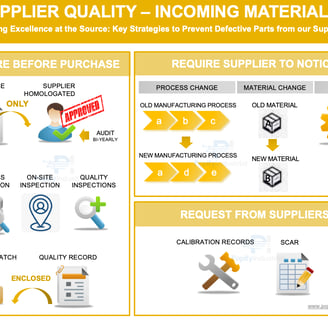
QUALITY SUPPLIER | KEY ROLES
Securing Excellence at the Source: Key Strategies to Prevent Defective Parts from Entering Our Supply Chain
In the realm of quality assurance, preventing defective parts from reaching our company is not just a preference; it's an absolute necessity. The following guidelines elucidate crucial steps to safeguard our production from supplier-related defects.
1. Supplier Homologation.
Homologate supplier to both the product itself (Product Homologation) and the manufacturing process responsible for its creation (Process Homologation).
Conduct bi-annual supplier process audits to ensure ongoing compliance and process capability.
Only place purchasing orders (POs) with suppliers who have received approval...
Please download the attached PDF or PPT to access the complete content.
Quality Supplier
Key Roles
Quality Supplier
Control Dashboard
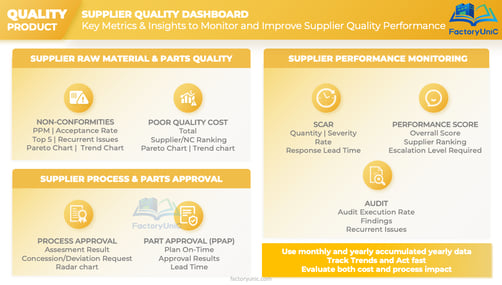
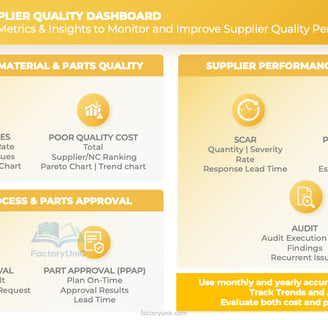
Quality Supplier | CONTROL Dashboard
A Strategic Dashboard to Control the Quality Enters Our Factory – and Protect What Leaves It
Overview
If you build products by assembling parts — quality starts long before assembly begins. It starts with what we receive, and more precisely, who we receive it from. Suppliers are an extension of our factory. If they underperform, it becomes our problem. If their parts fail, we take the hit — in rework, in downtime, and in customer complaints. That’s why this Supplier Quality Dashboard is not just another report. It is our early warning system, our accountability map, and our guide to better decisions.
1. SUPPLIER INCOMING PARTS & MATERIALS
Monitor where risk is increasing, where improvements are working, and where...
Please download the attached PDF or PPT to access the complete content.
Quallity Supplier
Supplier Approval (Homologation)
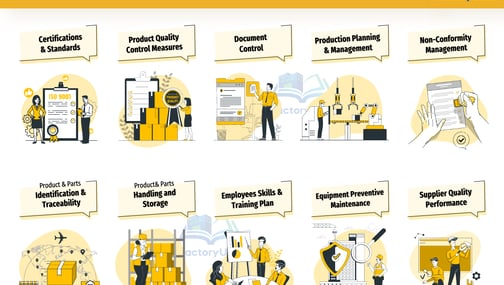
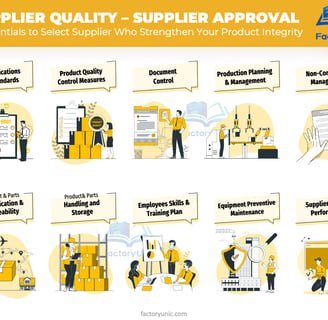
QUALITY SUPPLIER | SUPPLIER APPROVAL
Supplier Approval - The First Line of Defense for Quality Excellence
“Suppliers are not external resources — they are co-guardians of quality”
In the quality management, supplier approval (also known as “homologation”) plays a pivotal role in safeguarding product excellence
When considering the integration of a supplier into your network, several key factors demand meticulous evaluation due the suppliers are foundational pillar of our supply chain. These factors not only influence product quality but also determine the integrity and reliability of our supply chain. Here, we delve into the essential facets to contemplate during the supplier homologation process:
1. Certifications and Standards: Adherence to internationally recognized standards, such as ISO 9001 for Quality Management Systems, is a hallmark of commitment to quality excellence. Demand concrete evidence of compliance, such as certifications ...
Please download the attached PDF or PPT to access the complete content.
Quality Supplier
Supplier Quality Agreement
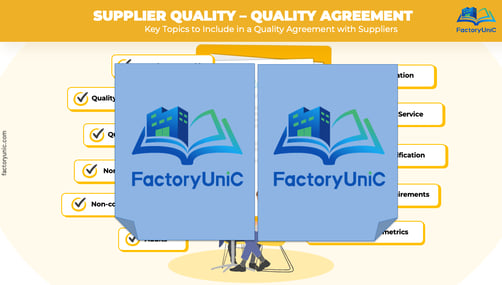
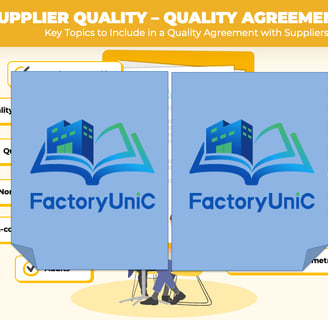
Quality Supplier | SUPPLIER Agreement
Establish clear quality agreements with suppliers, outlining the specific quality requirements and expectations to minimize risks. Key points to include in a supplier agreement:
Quality Records and Certificates: Require the supplier to provide detailed quality records and certificates for each batch sent, including quality checks, test results, inspections, and applied standards and Certificates such as CE Certification document. This ensures accountability, facilitates audits, and supports traceability.
Quality Assurance and Penalties: Establish a minimum level of quality that products must meet, with financial penalties or other corrective measures in case of non-compliance.
...
Please download the attached PDF or PPT to access the complete content.
Quality Control
Visual Quality Controls
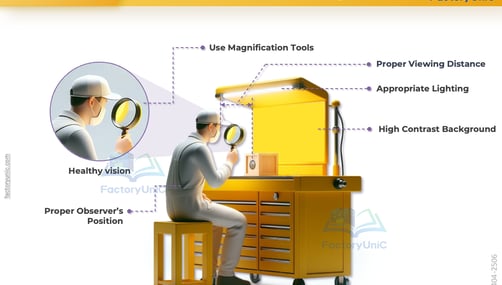
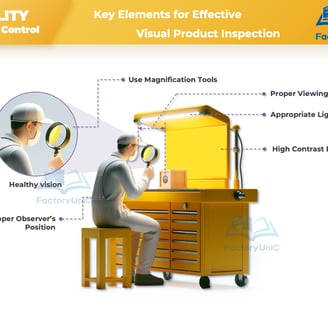
QUALITY CONTROL | VISUAL INSPECTION
WHAT KEY ELEMENTS SHOULD TO TAKE INTO CONSIDERATION FOR A SUPERIOR VISUAL PRODUCT INSPECTION?
In the realm of quality assurance, visual inspection remains a cornerstone. However, the effectiveness of this inspection hinges on several critical factors. Let’s delve into the essential elements that ensure precision and accuracy in visual product inspections.
1️⃣ Optimal Lighting Conditions 💡
Lighting can make or break an inspection process. Adequate illumination is vital, but it's a balancing act - too dim, and you miss the subtleties; too bright, and you're blinded by glare. The goal is clear, consistent lighting that accentuates product details without creating distracting shadows or glare. Adjustable lamps are recommended...
Please download the attached PDF or PPT to access the complete content.
Quality Supplier
Part Homologation Report Template
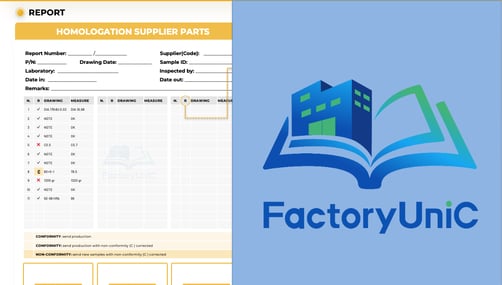
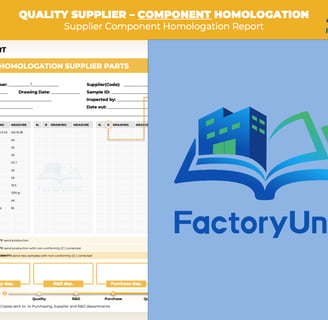
QUALITY SUPPLIER | Homologation Report Template
This document provides an example template for the verification and homologation of supplier components.
Such a template ensures that each piece meets precise technical specifications, maintaining the highest standards of reliability and performance.
Please download the attached PDF or PPT to access the complete content.
Quality Plant
Control Dashboard
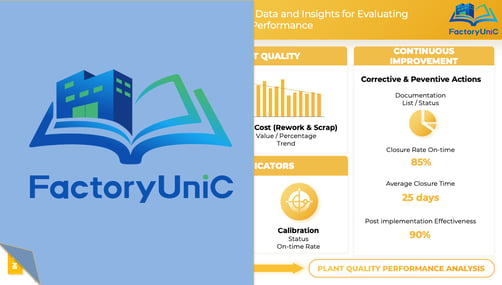
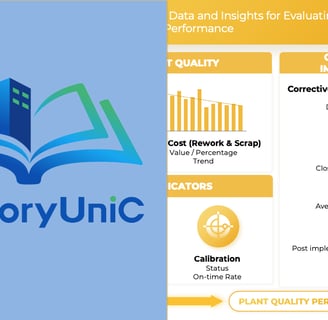
QUALITY PLANT | CONTROL DASHBOARD
Key Quality Metrics for Evaluating Plant Performance
In every manufacturing plant—whether you're assembling precision gearboxes, implantable medical sensors, or industrial control panels—quality isn’t just a department; it’s the foundation of trust, performance, and profitability. But quality doesn't improve by chance. It must be quantified, tracked, and continuously improved through disciplined data-driven action. Below are the essential indicators and information that every quality team member should know, understand, and monitor to drive excellence on the shop floor.
1.- In-Process & Final Product Quality Metrics
First Pass Yield (FPY). The percentage of units that pass all inspections the first time without rework...
Please download the attached PDF or PPT to access the complete content.
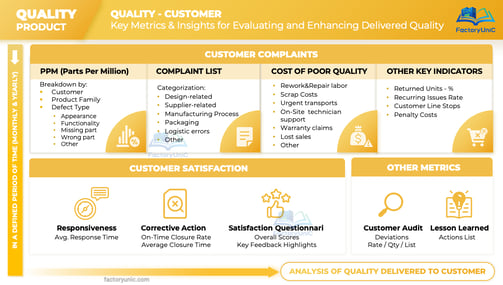
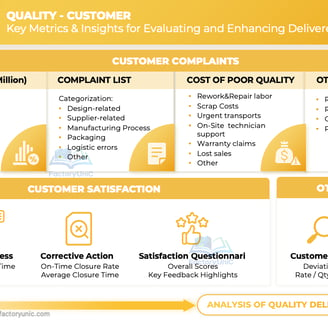
QUALITY CUSTOMER | CONTROL DASHBOARD
In manufacturing, quality delivered to the customer is more than a result—it's a promise. But how do we measure and improve that promise consistently? Through key performance indicators (KPIs).
1. Customer Complaints.
Every complaint is an opportunity—an insight into how we can do better.
1.1. PPM (Parts Per Million)
Formula: ...
Example: ...
Interpretation: ...
Others: It can be broken down by customer, product family, and defect...
Please download the attached PDF or PPT to access the complete content.
Quality Customer
Control Dashboard
Quality System
Contract Review
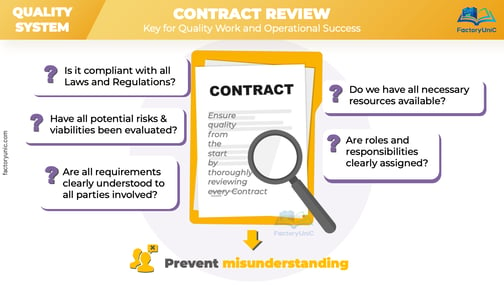
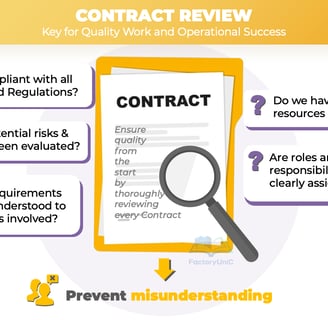
quality system | Contract Review
What is a Contract Review?
A Contract Review is the process of carefully checking agreements between your company and clients or suppliers to ensure that all requirements, expectations, and standards are clearly understood and achievable before starting any production or service.
Why is Contract Review Important?
Conducting a thorough Contract Review is vital because:
It prevents misunderstandings and disputes.
It ensures customer satisfaction...
Please download the attached PDF or PPT to access the complete content.