OPTIMIZATION TOOLS
The Optimization Tools section of FactoryUniC offers a set of powerful, practical resources in PDF and PPT formats designed to help industrial teams eliminate waste and boost performance. Every document is built for practical use—straightforward, grounded in operational expertise, and ready to help your team streamline with confidence.
Lean manufacturing
Waste of the Motion
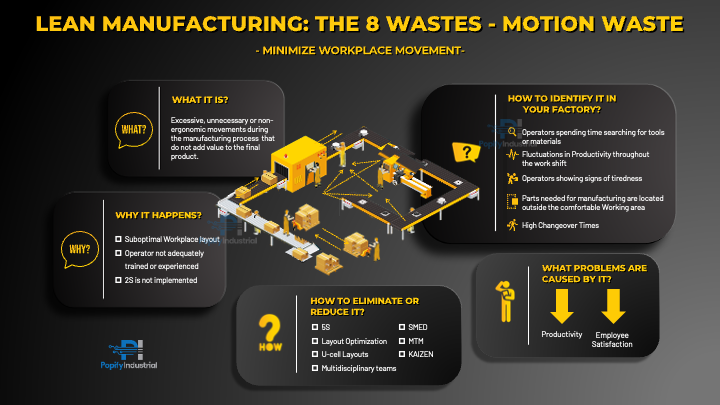
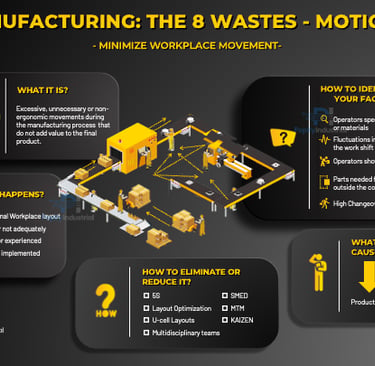
LEAN MANUFACTURING – WASTE 1 | Motion
What is it?
It refers to unnecessary or excessive or non-ergonomical physical movements during the manufacturing process by worker that do not add value to the final product.
Why does it happen?
Poor ergonomic workplace layout design and inefficient workspace organization.
Operators may not be adequately trained or experienced.
Absence of 2S (Set in order).
How to identify it? ...
Please download the attached PDF or PPT to access the complete content.
Lean manufacturing
Waste of the Overproduction
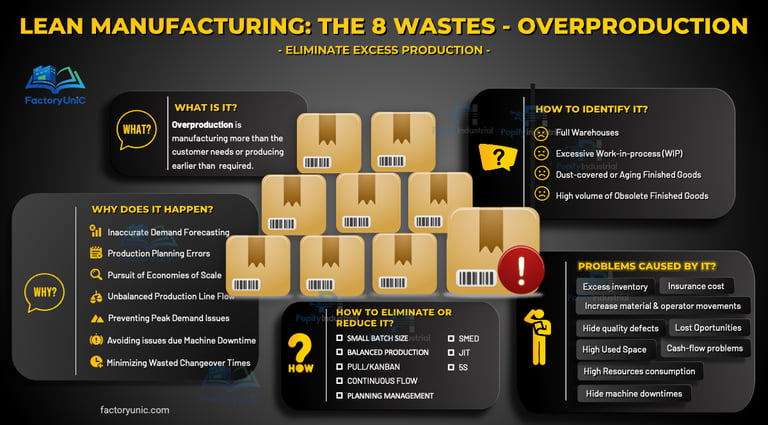
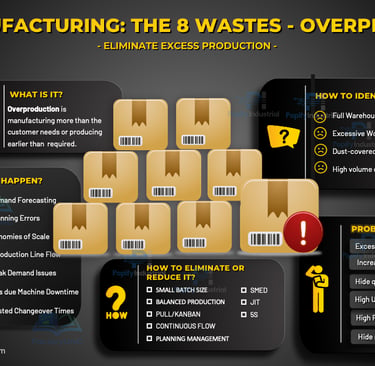
LEAN MANUFACTURING - WASTE 2 | Overproduction
What is it?
Overproduction is the act of producing more than is required, or producing earlier than it is needed. It is often considered the most detrimental of the Lean Manufacturing wastes because it can hide other wastes, such as defects, excess inventory, and unnecessary processing. Understanding and eliminating overproduction is key to optimizing operations and achieving lean excellence.
How to identify it?
Recognizing the signs of overproduction is the first step towards eliminating it:
Overstocked storage areas, ...
Please download the attached PDF or PPT to access the complete content.
Lean manufacturing
Waste of the Waitings
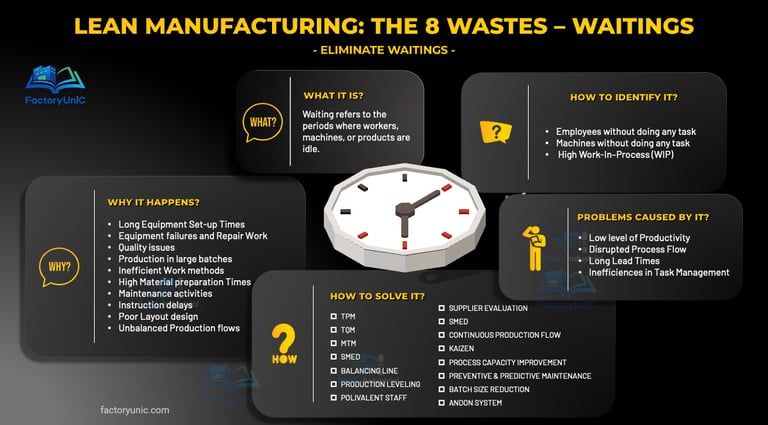
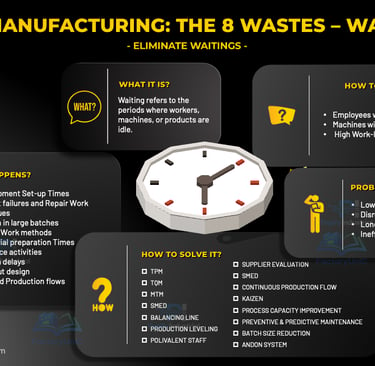
LEAN MANUFACTURING - WASTE 3 | Waitings
What is it?
The waste of waiting occurs when workers, machines, or products are left idle while waiting for materials, information, or the completion of another process.
Possible Causes?
Process and Equipment issues:
Equipment Setup and Adjust Times.
Equipment Failures and Repairs
Maintenance Activities: Scheduled and unscheduled maintenance stoppages, ...
Please download the attached PDF or PPT to access the complete content.
Lean manufacturing
Waste of the Overprocessing
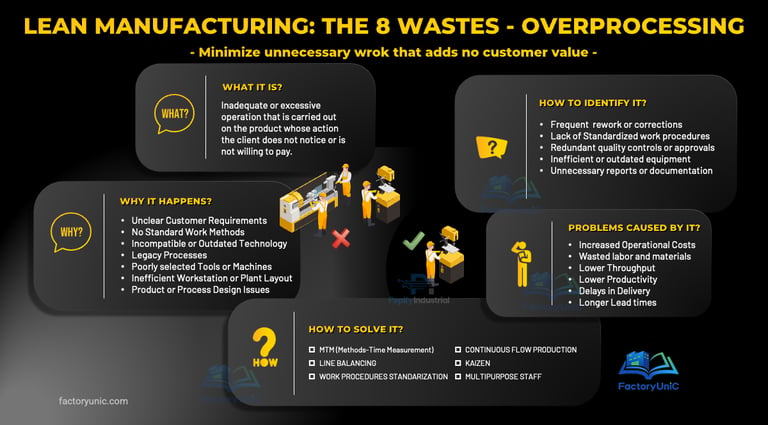
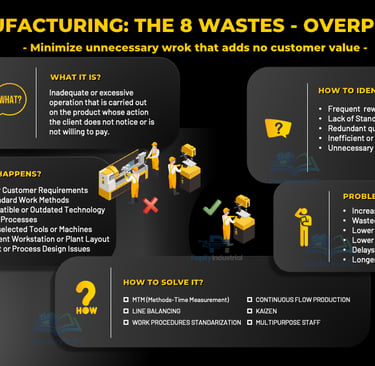
LEAN MANUFACTURING - WASTE 4 | Overprocessing
What is it?
Overprocessing is performing more work on a product or service than what is required by the customer. Below are some examples:
❌ Applying extra layers of paint or high polishing of hidden parts.
❌ Check the dimensions of a part that are already ensured by machine.
❌ Using more packaging materials than necessary.
❌ Machining parts to strict tolerances where standard precision would suffice.
❌ Re-entering the same data in different systems.
“If the customer doesn’t notice it—or won’t pay for it—then you’re doing too much.”
...
Please download the attached PDF or PPT to access the complete content.
Lean manufacturing
Waste of the Excess of Transportation

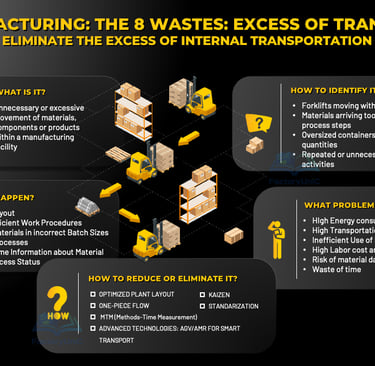
LEAN MANUFACTURING - WASTE 5 | Excess of Transportation
What is it?
Excessive internal transportation refers to the unnecessary or inefficient movement of materials, semi-processed products and products within the manufacturing facility. This waste is closely linked to the ”motion" waste but transport is referred to the movement of materials and products while the motion refers to the movement of the people inside a working area.
Why does it happen?
Poorly designed facility layouts or obsolet layouts often require materials and products to travel longer distances than necessary.
Lack off/unclear standardized work processes can lead to inconsistent and inefficient material handling practices.
...
Please download the attached PDF or PPT to access the complete content.
Lean manufacturing
Waste of the Quality Defects and Reworks
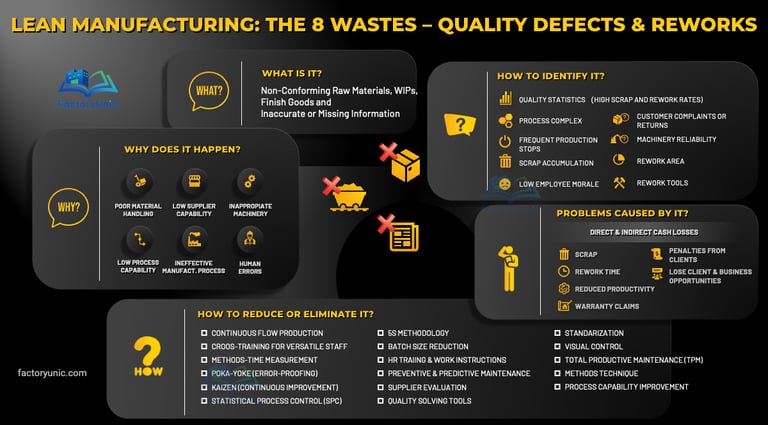
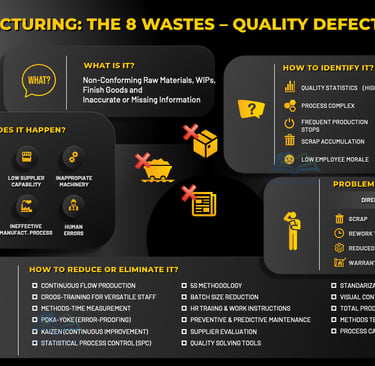
LEAN MANUFACTURING - WASTE 6 | Quality Defects and Reworks
What is it?
It refers to anything that falls below the expected quality standards – from raw materials and work-in-progress to finished goods and even data inaccuracies. Examples:
❌ A part that doesn’t fit because it was cut too short
❌ A label printed with the wrong date
❌ A machine that makes 1 out of 10 parts with a crack
How to Identify it?
👉 Quality Statistics: High defect rates or rework percentages.
👉 Frequent Production Stops: Interruptions in the flow due to quality issues.
...
Please download the attached PDF or PPT to access the complete content.
Lean manufacturing
Waste of the Unused Talent
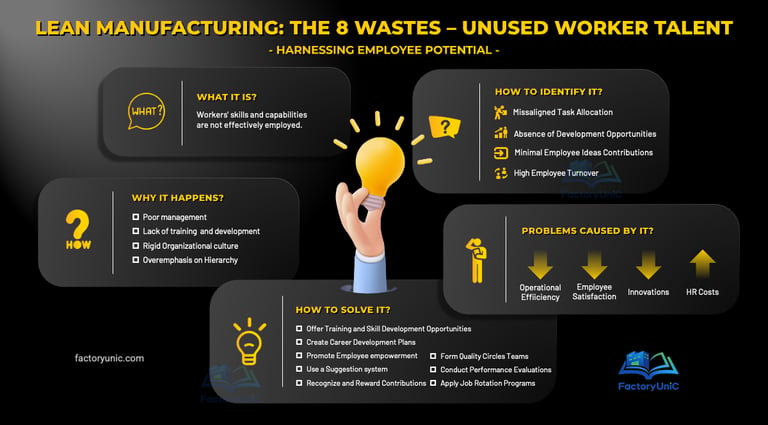
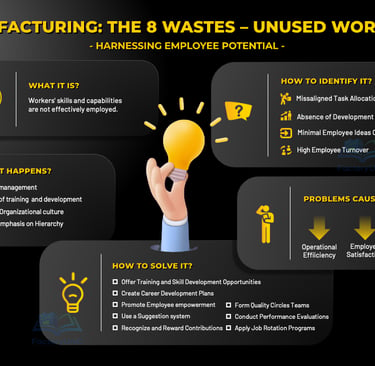
LEAN MANUFACTURING - WASTE 8 | Unused Talent
What is it?
It refers to underutilized talent waste occurs when workers' skills, knowledge, and creativity are not effectively employed.
How to Identify It?
👉 Employees are assigned tasks that don't match their skill levels or expertise.
👉 Lack of training and career development opportunities for employees.
👉 Few or no mechanisms for workers to share ideas or contribute to process improvements.
👉 High Employee Turnover.
Please download the attached PDF or PPT to access the complete content.
5S methodology
5S (A small book about 5S, 8 slides)
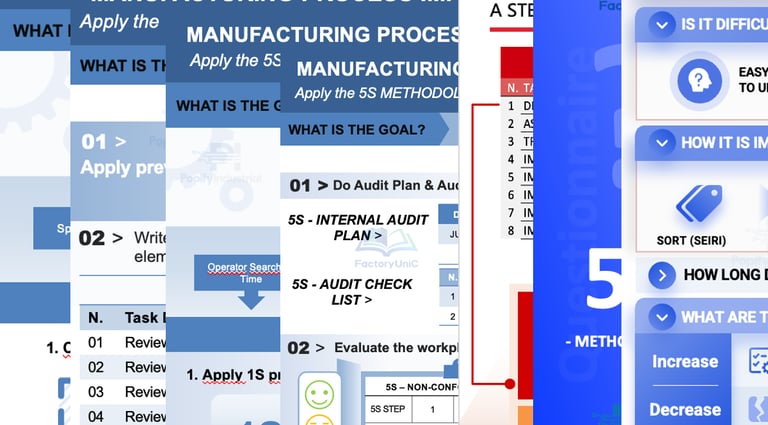
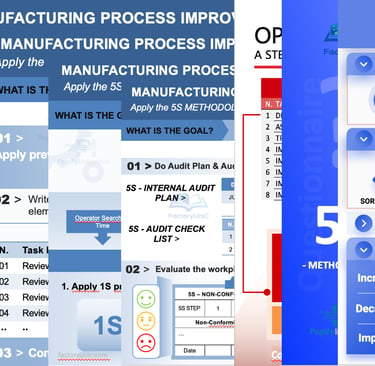
5S METHODOLOGY
What is it?
The 5S methodology is a powerful tool that should be implemented as THE FIST STEP in any factory seeking to improve its manufacturing process.
The 5S methodology consists of five steps, each represented by a Japanese word starting with the letter "S":
Step 1: Seiri (Sort): Separate or eliminate unnecessary items from the workplace.
Step 2: Seiton (Set in Order): Organize the workplace efficiently.
Step 3: Seiso (Shine): Improve the level of cleanliness in the workplace.
Step 4: Seiketsu (Standardize): Establish standardized practices to maintain the first three S’s.
Step 5: Shitsuke (Sustain): Create a habit, a culture of discipline and...
Please download the attached PDF or PPT to access the complete content.
Visual Factory
Andon System
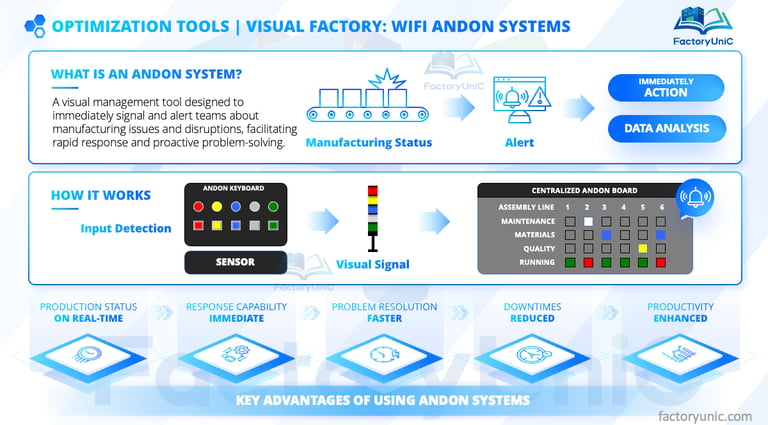
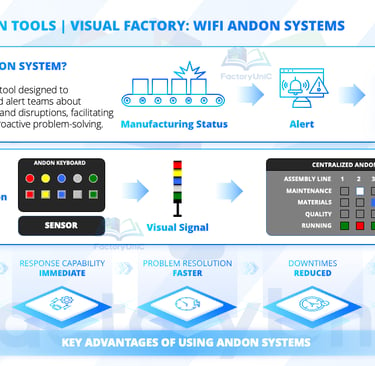
OPTIMIZATION TOOLS | VISUAL FACTORY: ANDON SYSTEMS
What is an Andon System?
Andon (a Japanese word meaning "lamp") is a simple but powerful visual management tool (device) widely utilized in factories. It helps workers and supervisors know immediately when something goes wrong in production—like a machine stopping, materials shortages, or a quality problem. It uses lights, sounds, and even phone alerts to communicate these issues clearly and quickly. 🌟
How the Andon System Works?
1.- Detection & Activation.
Each production line or workstation has a small box with buttons (called an Andon box) or sensors...
Please download the attached PDF or PPT to access the complete content.
Visual Factory
Floor Marking
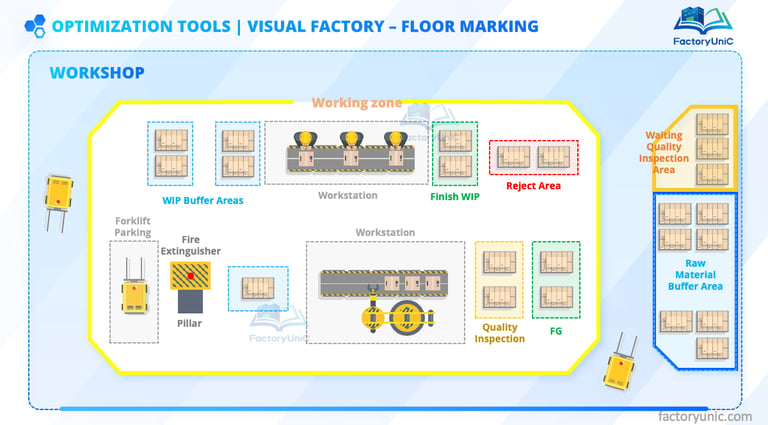
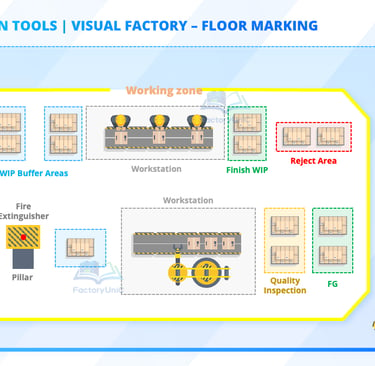
VISUAL FACTORY: FLOOR MARKING: COLOUR AND LINE WIDTH GUIDELINES✨
What Is Floor Marking in a Visual Factory?
Floor marking is a visual management technique used to organize space and improve safety, efficiency, and communication on the shop floor. Colored lines, zones, and labels guide the movement of people, materials, and equipment—making everything visible and easy to understand at a glance.
This document provides a practical guide for applying floor markings using colours and line widths.
Advantages of Floor Marking Systems
1. Enhanced Workplace Safety
Visually distinguishes hazardous zones and defines access to emergency....
Please download the attached PDF or PPT to access the complete content.
Quality Methodology
Poka-Yoke
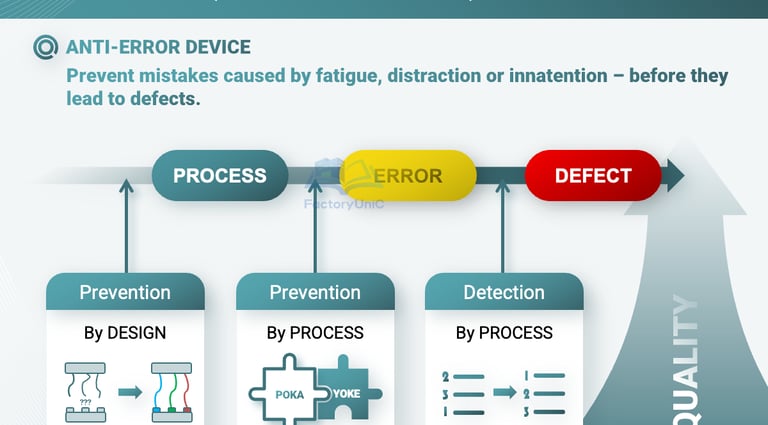
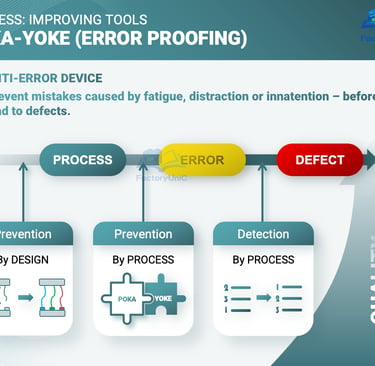
POKA-YOKE: A SMART AND SIMPLE WAY TO PREVENT MISTAKES
What is Poka-Yoke?
It is a device or method that eliminates any possibility that the operator can make mistakes, due to fatigue or distraction, which implies defective products. Its key role is to ensure 100% verification before the process continues.
These mistakes can be, among others:
Product with Missing Part.
Product with Wrong Part Assembled.
Manufacturing Process Steps missed or incorrectly done.
Wrong Setup of Machines or Equipment.
Please download the attached PDF or PPT to access the complete content.